Einsatz von Werkzeugen
Durchmesser und Betriebsparameter der Werkzeuge sind einfach einzustellen und anzupassen. Die Variablen Zugabe, Vorschub und Geschwindigkeit sind vor dem Vorgang einzustellen.
Das Glattwalzverfahren verursacht keine Änderung des Werkstückvolumens. Da der Werkstoff aber verschoben wird, verändert sich geringfügig der Durchmesser. Beim Glattwalzen eines symmetrischen Oberflächenprofils verändert sich der Durchmesser höchstens um die Höhe von der Spitze bis zum Untergrund. Diese Tatsache muss bei der vorangehenden zerspanenden Bearbeitung berücksichtigt werden, dabei muss eine entsprechende Menge Werkstoff erhalten bleiben, um die Maßänderung auszugleichen.
(Zeichnung 1) Hier sind allgemeine Anforderungen an die max. Zugabe für unterschiedliche Durchmesser dargestellt
Spanlose Oberflächenendbearbeitung & Kaltbearbeitung
Beim Glattwalzen handelt es sich um ein spanloses Verfahren der Oberflächenendbearbeitung. Durch den durch die Rollen erzeugten Druck auf die bearbeitete Oberfläche wird ein mikroskopischer Materialüberschuss in die Profiltäler verdrängt. (Zeichnung 3)
Das Glattwalzen im Kaltverfahren dient zur Bearbeitung von Metalloberflächen, damit man eine einheitliche, dichte und mikrostukturelle Oberflächenendbearbeitung erzielen kann. Der Tatsache, dass sie keinen Werkstoff abtragen – dh., keine Späne bilden – verdanken die Werkzeuge ROBUTO® ihre vielen Vorzüge, von denen die meisten bei anderen Endbearbeitungsvorgängen, z.B. Aufbohren, Drehen und Schleifen, nicht erzielt werden können.
Die spanlose Endbearbeitung – der Glattwalzvorgang im Kaltverfahren – wirkt auf die Metalloberfläche mit relativ geringen Kräften. Diese Kräfte überschreiten geringfügig die Dehngrenze des Werkstoffs und verursachen somit die plastische Verformung des Oberflächenmaterials. Da die plastische Verformung unterhalb der Kristallisationstemperatur erfolgt, wird diese Methode auch als Bearbeitung im Kaltverfahren bezeichnet.
Minimale Rauheit (Ra)
In der Tabelle Nr. 2 sind Rauheitswerte (Ra) für unterschiedliche Werkstoffe angegeben.
Aorteile
Erhöhte Beständigkeit gegen Materialermüdung
Da durch Ermüdung verursachte Schwachstellen sofort auftreten und ernste Schäden verursachen, sind sofortige Hilfsmaßnahmen einzuleiten. Metallelemente können auch dann beschädigt werden, wenn die eingesetzten Kräfte weit unterhalb der Dehngrenze liegen. In der Praxis hat sich herausgestellt, dass Einschnitte, scharfe Querschnittsänderungen und sonstige spannungserhöhende Formen für Metalloberflächen gefährlich werden, wenn dynamische Kräfte eingesetzt werden.
Das Glattwalzverfahren dient zum Glätten von scharfen Rauheitsspitzen, z.B. Einschnitten und Werkzeugspuren. Ein anderer und weit wichtigerer Aspekt ist die Tatsache, dass das Glattwalzverfahren die schädliche Wirkung der dynamischen Kräfte verringert und eine restliche Druckeigenspannung auf der Werkstückoberfläche erzeugt.
Nach dem Glattwalzverfahren verformt sich das Material auf einer bestimmten Tiefe unterhalb der Oberfläche plastisch und versucht, sich zurückzuformen. Dabei werden Pressspannungen auf der Oberfläche und Zugspannungen im plastisch verformten Bereich erzeugt. Das führt zur Erhöhung der Materialbeständigkeit gegen Ermüdung, weil alle äußeren Kräfte zuerst die entstandenen Restspannungen bewältigen müssen.
Diese zwei, oben beschriebenen Ergebnisse des Glattwalzverfahrens (Eliminierung von Rauheitsspitzen und Erzeugung von restlicher Druckspannung) erhöhen die Ermüdungsfestigkeit bis zu 300%.
Bearbeitungsvorgang – Verfestigung
Das Glattwalzgerät presst und drückt das Werkstück zusammen, wenn es mit dem Werkzeug in Berührung kommt.
Dabei wird die Kornstruktur geändert und ein Teil davon verfestigt. Durch die Verschiebung der Körner und ihre Verformung ändert sich ihre Größe, dabei erhöht sich das Grenzvolumen infolge des Kaltverfahrens.
Da man es in diesem Fall mit einer Oberflächenhärte zu tun hat, kann man diesen Parameter nicht mit herkömmlichen Härteprüfungen untersuchen, z.B. nach Rockwell oder Brinell. In diesem Fall wird die Tukon-Härteprüfung durchgeführt. Die Knoop-Härte wird mit Hilfe dieser Untersuchung ermittelt. Den auf diese Weise ermittelten Wert kann man in den Härtewert nach Brinell bzw. Rockwell umrechnen.
Die Härteprüfung nach Knoop zeigt eine wesentliche Erhöhung der Oberflächenhärte, dabei verringert sie sich bei größerer Entfernung von der Oberfläche bis auf den ursprünglichen Wert. Auf der Zeichnung Nr. 5 ist das Verhältnis der Oberflächenhärte zu Eindringtiefe (Entfernung zur Oberfläche) dargestellt.
Die Erhöhung der Oberflächenhärte für unterschiedliche Werkstoffe ist in der Tabelle Nr. 3 dargestellt
Korrosion und Porosität
Dank dem Glattwalzverfahren wird die Korrosionsfestigkeit des Werkstückes erhöht. Die Eliminierung von Rauheitsspitzen, Rissen und Poren, an bzw. in denen sich reaktive Stoffe und Schmutzpartikel ablagern können, trägt zu einer hohen Korrosionsbeständigkeit bei.
Auf dem Werkstück kann es zu Rissbildung kommen, wenn es reaktiven Stoffen und Restspannungen ausgesetzt ist. Risse, die durch eine Wechselwirkung von statischen Zugspannungen in der Metallschicht und korrosionsbildenden Faktoren entstehen, nennt man Spannungskorrosion. Beim Glattwalzen werden Zugspannungen eliminiert, wenn das Material einer Druckwirkung ausgesetzt ist, weil restliche Druckspannung auf der Werkstückoberfläche erzeugt wird.
Das Glattwalzverfahren beseitigt wirksam die oben angeführten Faktoren, die durch Korrosionsspannungen verursachte Risse hervorrufen.
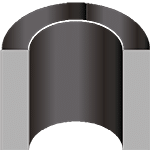
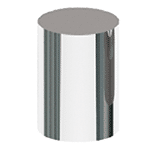
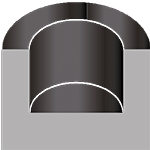
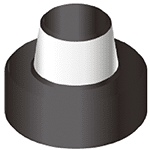
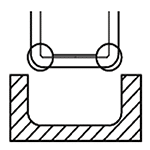
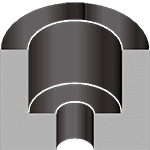
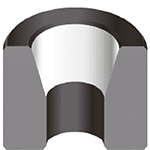
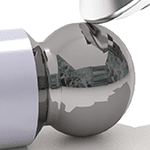
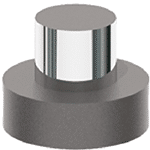
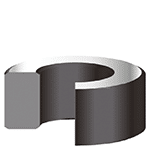
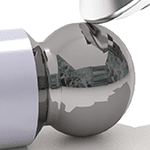
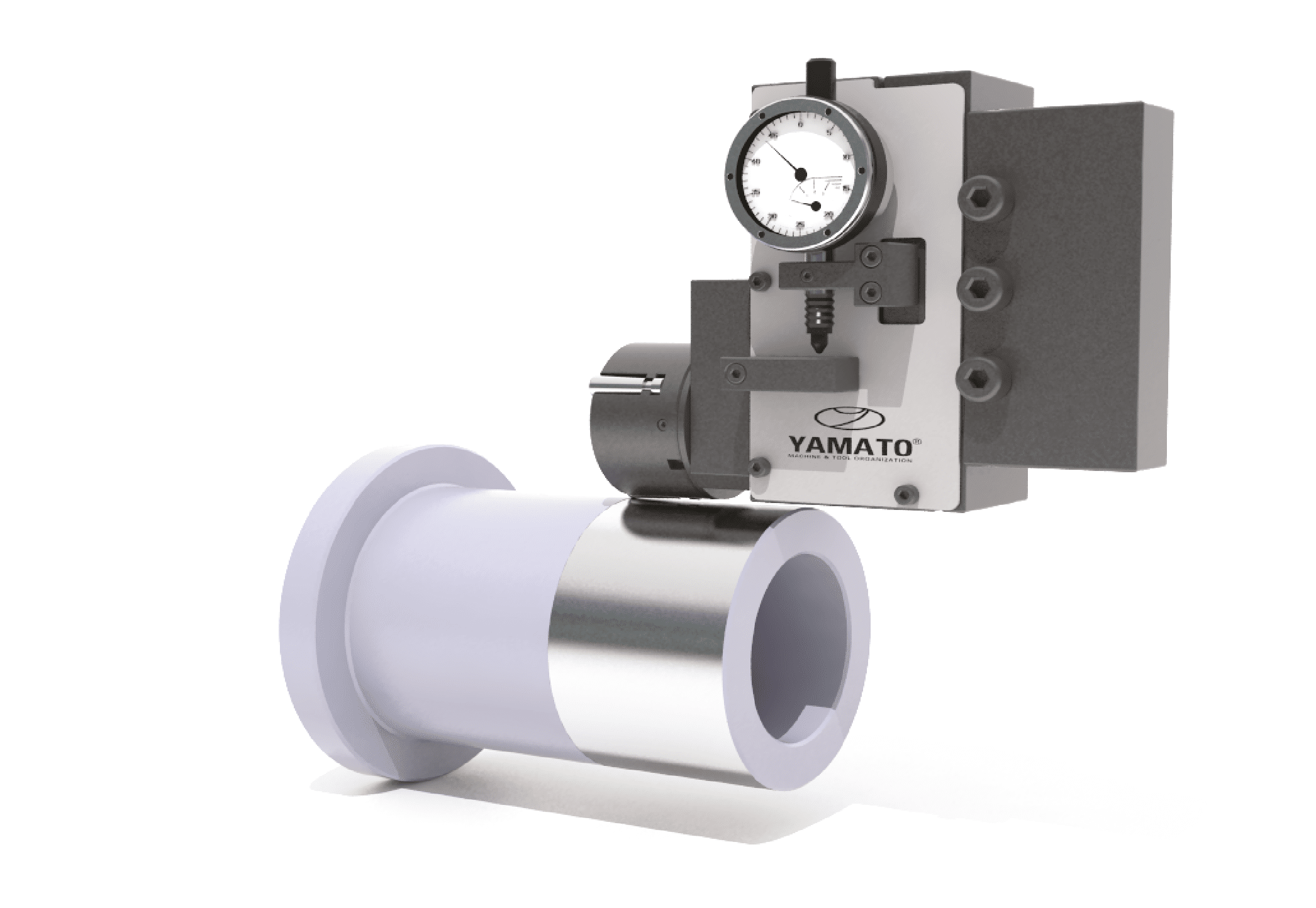
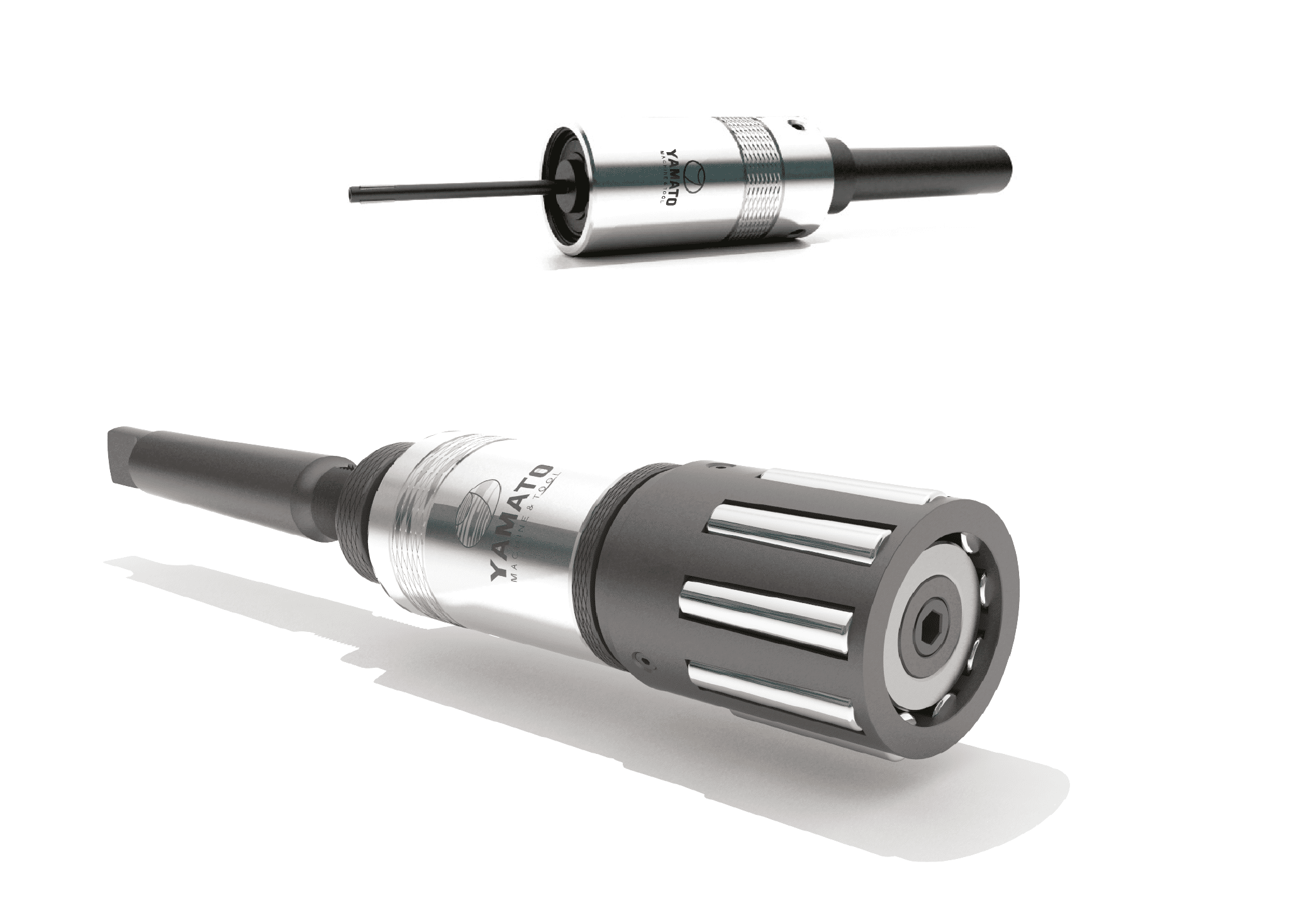
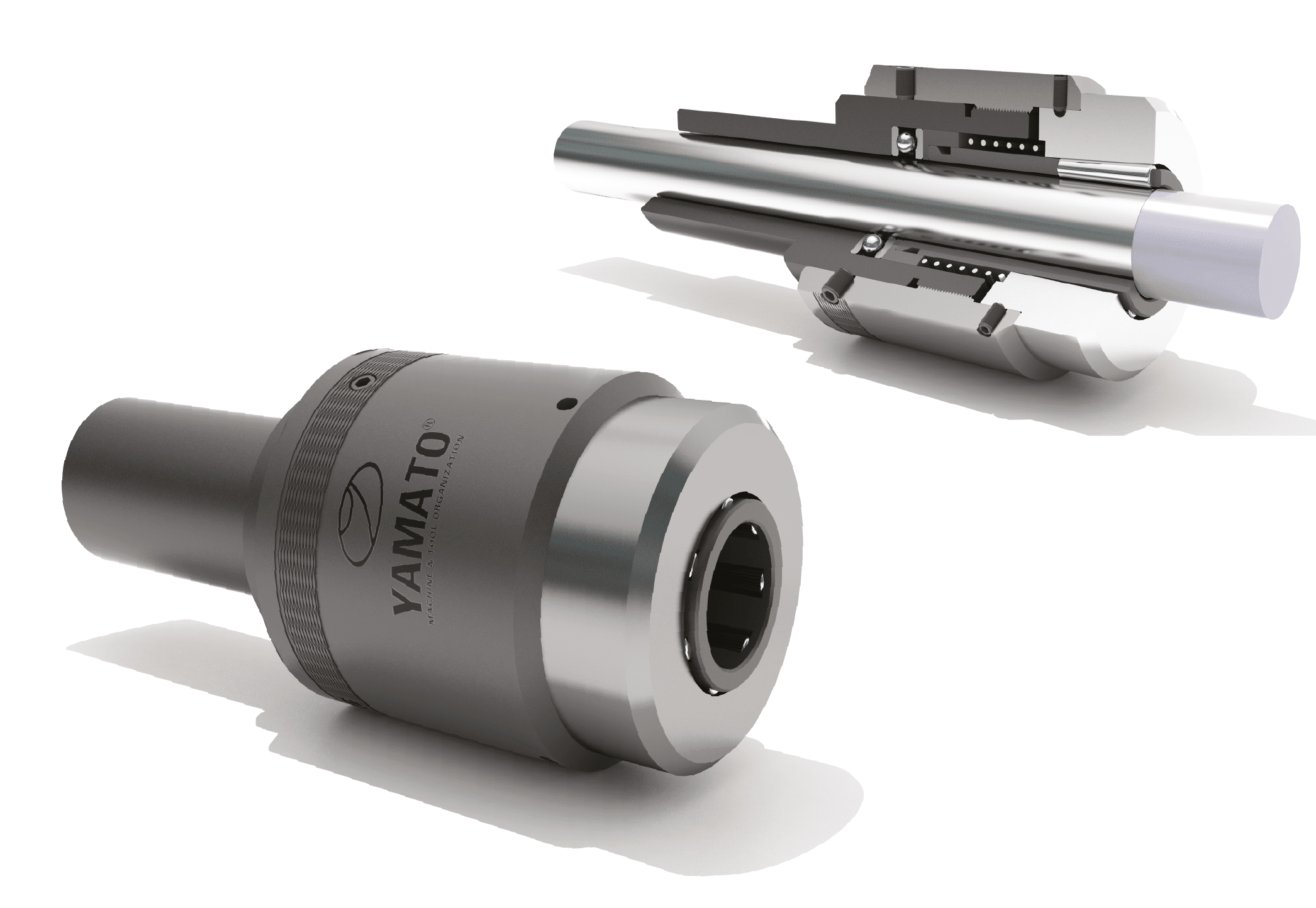